1. Description
This series of addition-cure (platinum-catalyzed) silicone is a medium-hardness, flexible elastomeric material. Both Part A and Part B are translucent viscous liquids that can be colored with silicone pigments to achieve a wide range of colors. After mixing the two parts in a 1A:1B weight or volume ratio, curing can be completed at room temperature within several hours or accelerated by heating.
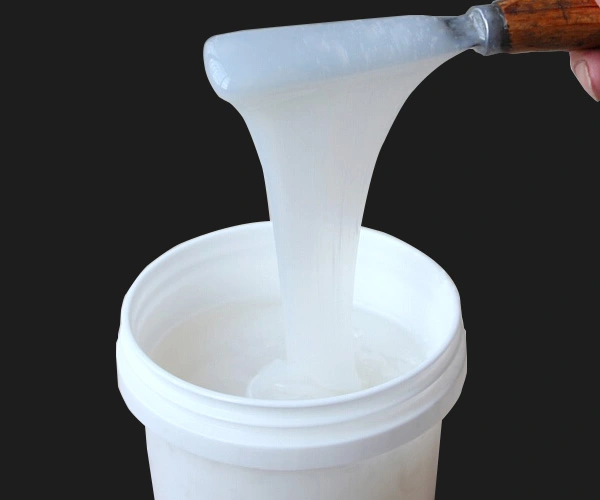
2. Feature
- 1A:1B ratio, easy to use.
- It has good flexibility and elasticity.
- High tear strength and excellent elongation.
- Very low shrinkage for extremely accurate molds.
- Heat resistant up to 250°C (482°F).
- It reproduces fine details accurately.
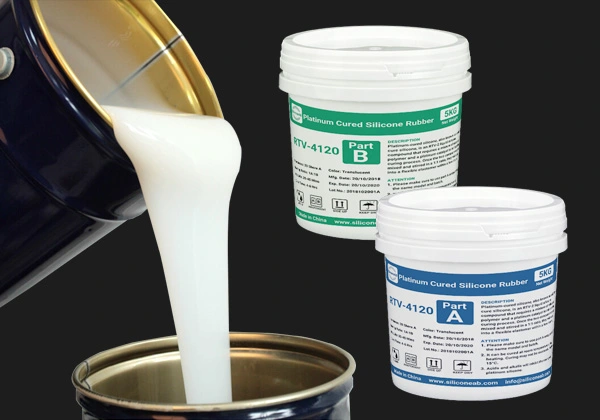
3. Application
This medium-hardness platinum-cured silicone rubber is a high-performance material with excellent tear strength, tensile strength, elongation, low shrinkage rate, and accurate detail reproduction. They are very suitable for mold making in various materials and industries, ranging from epoxy resin, polyester, cement, concrete, gypsum, to low-melting point metals that require heat resistance.
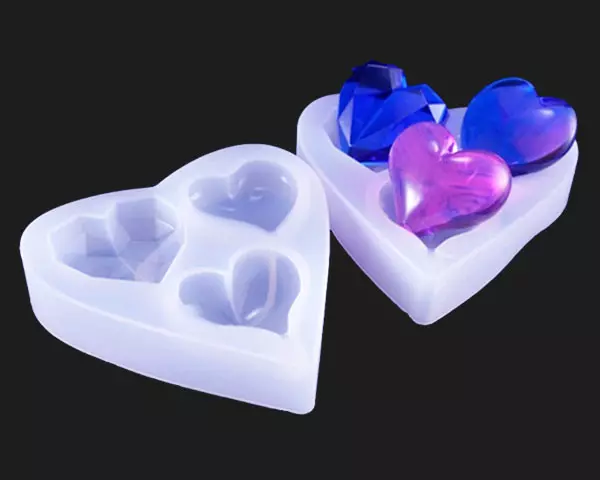
Resin Silicone Mold
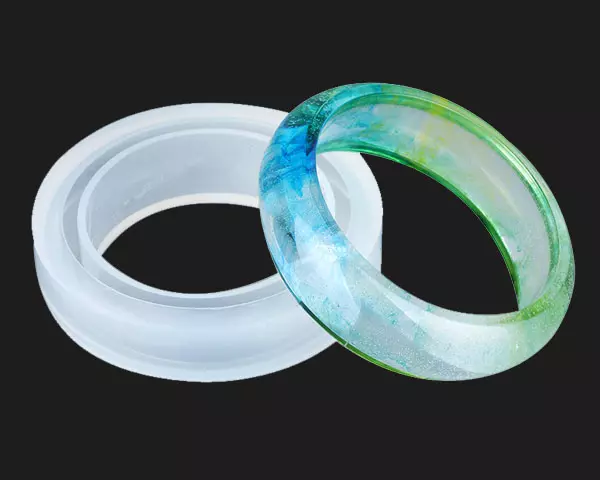
Resin Bracelet Mold
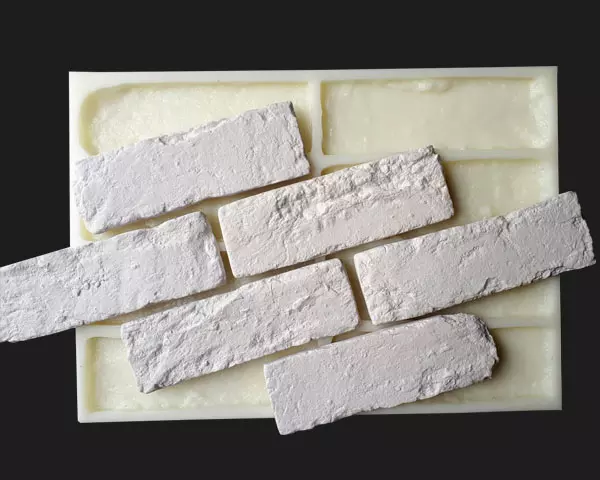
Cultural Brick Mold
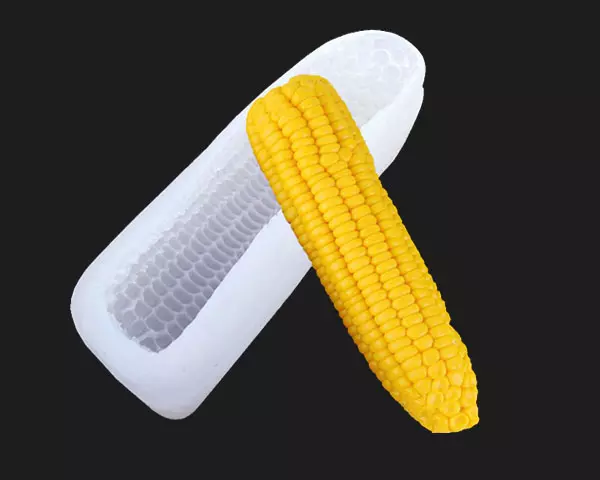
Simulation Corn Mold
4. Attention
- Please use parts A and B of the same model and lot number. If different batches are used, suitability should be determined by testing.
- For optimal results, mix and cure the material at 20-30°C (68-86°F) and 50% relative humidity. Addition-cured liquid silicone should not be used in humid conditions, as this may cause defective curing.
- Lower temperatures and humidity will increase the working time of the material. Do not use platinum-cured silicone at temperatures below 15°C (60℉), as it may not cure properly or may be difficult to cure at all.
- Platinum-cured liquid silicone needs to be used with care to avoid inhibition. Inhibition occurs when the platinum cure silicone doesn't fully cure due to contamination on the surface of the object being molded. Although it may appear to be fully cured on the surface, a tacky surface will be present after separation - this is called inhibition. Amines, tin compounds, sulfur-based clay, newly cast polyester, natural rubber such as latex and rubber gloves, PVC stabilizers, epoxy resin catalysts, UV curable resin, or urethane rubber may cause inhibition. If compatibility between the addition cure silicone and the surface is a concern, it is recommended to perform a small-scale test. Do not smoke during operation.
5. Safety
- Under normal storage and handling conditions, these products are stable in airtight containers at room temperature and will not undergo any hazardous reactions.
- Please keep out of reach of children.
- First Aid Measures:
- Skin Contact: Wash the affected skin thoroughly with soap and water. Seek medical attention if symptoms persist after washing.
- Eye Contact: In the event of contact with the eyes, rinse them thoroughly with clean water for at least 15 minutes. Seek medical attention if irritation persists after rinsing.
- Inhalation: Under normal conditions of intended use, this material is not expected to be an inhalation hazard.
- Ingestion: Do not induce vomiting unless instructed by a physician. Rinse mouth thoroughly. Seek medical attention if symptoms occur.
Please note that these measures are general guidelines. In case of an emergency, always consult a medical professional or seek immediate medical attention.
6. Storage
When stored at room temperature (15 to 25°C / 60 to 77°F), the material has a shelf life of 12 months from the date of manufacture. Storing the material at higher temperatures may shorten the usable shelf life of unused materials. However, storing the product beyond the specified date on the certificate of analysis does not necessarily mean that the product is no longer usable.
Containers that have been opened must be carefully resealed to prevent leakage. Store in a cool, dry place with adequate ventilation and keep away from incompatible materials (such as bases and acids), open flames, and high temperatures.